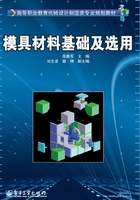
1.2 知识准备
1.2.1 模具及模具材料分类
1.模具的分类
为了便于模具材料的选用,通常根据工作条件将模具分为冷作模具、热作模具和型腔模具三大类。
(1)冷作模具。根据工艺特点,可将冷作模具分为冷冲裁模具和冷变形模具两类。冷冲裁模具主要包括各种薄板冷冲裁模具和厚板冷冲裁模具。冷变形模具主要包括各种冷挤压模具、冷镦模具、冷拉深模具和冷弯曲模具等。
(2)热作模具。热作模具可分为热冲切模具、热变形模具和压铸模具三类。热冲切模具包括各种热切边模具和热切料模具。热变形模具包括各种锤锻模具、压力机锻模具和热挤压模具。压铸模具包括各种铝合金压铸模具、铜合金压铸模具及黑色金属压铸模具等。
(3)型腔模具。根据成形材料的不同,可将型腔模具分为塑料模具、橡胶模具、陶瓷模具、玻璃模具、粉末冶金模具等。
2.模具材料的分类
能用于制造模具的材料很多,通常可分为钢铁材料、非铁金属和非金属材料三大类,目前应用最多的还是钢铁材料。
(1)钢铁材料。用于制造模具的钢铁材料主要是模具钢。通常将模具钢分为冷作模具钢、热作模具钢、塑料模具钢三类。
(2)非铁金属材料。用于制造模具的非铁金属材料主要有铜基合金、低熔点合金、高熔点合金、难熔合金、硬质合金、钢结硬质合金等。
(3)非金属材料。用于制造模具的非金属材料主要有陶瓷、橡胶、塑料等。
由于模具钢是制造模具的主要材料,一般将模具材料分类如图1-1所示。

图1-1 模具材料分类图
1.2.2 模具材料的性能要求
模具在现代工业中得到广泛应用。模具直接关系到产品的质量、性能、生产率及成本,而且模具的质量和使用寿命与制造模具的材料及工艺有着密切的关系。因此,需要了解模具材料的主要性能指标。
1.硬度和热硬性
材料抵抗其他硬物压入表面的能力称为材料的硬度。从本质上说,硬度并不是材料的一个新的特殊性能,而是代表材料的弹性、塑性、韧性和形变硬化等的一个综合性能。它反映材料抵抗局部塑性变形的能力。由于大多数常用钢材的强度与硬度之间有一定的近似比例关系,根据硬度可以大致估计材料的抗拉强度。另外,材料的抗磨损性能与其硬度有密切的关系,所以,金属材料的硬度也是金属力学性能的重要指标之一。
目前,用于测定材料硬度的方法有三种:布氏硬度法、洛氏硬度法和维氏硬度法。三种方法都是采用一定形状的特制压头,在一定的载荷作用力下,压入被测材料的表面并保持一定时间,然后卸除载荷力,这样就在材料表面留下了一个一定尺寸的压痕。测量压痕尺寸的大小并根据载荷力的大小,就可以计算出该材料的硬度值。
1)布氏硬度
布氏硬度试验用的压头是淬火钢球,钢球直径有2.5mm、5mm和10mm三种。根据被测试材料的种类、硬度范围和试件厚度的不同,测定时所选用的钢球直径、载荷作用力大小和载荷保持时间也就不一样。
布氏硬度的试验原理如图1-2所示。将直径为D的钢球或硬质合金球,在一定载荷P的作用下压入试样表面,保持一定时间后卸除载荷,所施加的载荷与压痕表面积的比值即为布氏硬度。布氏硬度值可通过测量压痕平均直径d查表得到。

图1-2 布氏硬度的实验原理
当压头为钢球时,布氏硬度用符号HBS表示,适用于布氏硬度值在450以下的材料。压头为硬质合金时用符号HBW表示,适用于布氏硬度在650以下的材料。符号HBS或HBW之前的数字表示硬度值,符号后面的数字按顺序分别表示球体直径、载荷大小及载荷保持时间。如120HBS10/1000/30表示直径为10mm的钢球在1000 kgf(9.807 kN)载荷作用下保持30 s测得的布氏硬度值为120。
布氏硬度的优点是测量误差小、数据稳定;缺点是压痕大,不能用于太薄件或成品件。最常用的钢球压头适于测定退火钢、正火钢、调质钢、铸铁及有色金属的硬度。
2)洛氏硬度
洛氏硬度的试验原理如图1-3所示。在初载荷和总载荷(初载荷与主载荷之和)的先后作用下,将压头(金刚石圆锥体或钢球)压入试样表面,保持一定时间后卸除主载荷,用测量的残余压痕深度增量h1-h0计算硬度值(h0为初载荷压入的深度,h1为卸除主载荷后残余压痕的深度)。洛氏硬度用符号HR表示,根据压头类型和主载荷不同,分为九个标尺,常用的标尺为A、B、C,见表1-1。符号HR前面的数字为硬度值,后面为使用的标尺,如50HRC表示用C标尺测定的洛氏硬度值为50。

图1-3 洛氏硬度的试验原理
实际测量时,硬度值可从洛氏硬度计的表盘上直接读出。洛氏硬度的优点是操作简便、压痕小、适用范围广。缺点是测量结果分散度大。
表1-1 常用洛氏硬度的符号、试验条件及应用
3)维氏硬度
维氏硬度的试验原理如图1-4所示。将顶部两相对面具有规定角度(136°)的正四棱锥体金刚石压头在载荷P的作用下压入试样表面,保持一定时间后卸除载荷,所施加的载荷与压痕表面积的比值即为维氏硬度。维氏硬度可通过测量压痕对角线长度d查表得到。维氏硬度用符号HV表示,符号前的数字为硬度值,后面的数字按顺序分别表示载荷值及载荷保持时间。如640HV30/20表示在30 kgf(294.2 N)载荷作用下保持20 s测定的维氏硬度值为640。根据施加的载荷范围不同,规定了三种维氏硬度的测定方法,见表1-2。
维氏硬度保留了布氏硬度和洛氏硬度的优点,既可测量由极软到极硬的材料的硬度,又能互相比较。既可测量大块材料、表面硬化层的硬度,又可测量金相组织中不同相的硬度。
硬度实际上是一种综合的力学性能,模具材料的各种性能要求,在图样上只通过标注硬度来表示。作为成形用的模具应具有足够高的硬度,才能确保使用性能和使用寿命。如冷作模具一般硬度在52~60HRC范围内,而热作模具硬度一般在40~52HRC范围内。

图1-4 维氏硬度的试验原理
表1-2 维氏硬度的测定方法(GB/T4340.1-1999)
热硬性是指模具在受热或高温条件下保持高硬度的能力。多数热作模具和某些冷作模具,应具有一定的热硬性,才能满足模具的工作要求。
钢的硬度和热硬性主要决定于钢的化学成分、热处理工艺,以及钢的表面处理工艺。
2.耐磨性
模具在工作中承受很大的摩擦,从而导致模具工作面磨损。所以,耐磨性能是衡量模具使用寿命的重要指标。
模具的磨损形式很复杂,主要有磨粒磨损、黏着磨损、氧化磨损和疲劳磨损等。如冷作模具的磨损形式通常是磨粒磨损和黏着磨损,而热作模具的磨损形式主要是氧化磨损。
磨损形式不同,影响耐磨性的因素也各不相同。一般情况下,主要的影响因素是硬度和组织。当冲击载荷较小时,耐磨性与硬度成正比关系;当冲击载荷较大时,表面硬度越高并非耐磨性越好,超过一定的硬度值之后耐磨性反而下降。在钢的组织中,铁素体的耐磨性最差、马氏体的耐磨性较好、下贝氏体的耐磨性最好。另外,碳化物的性质、数量和分布状态对耐磨性也有显著的影响。
3.强度和塑性
评价材料强度和塑性最简单有效的办法就是测定材料的拉伸曲线。在标准试样(见图1-5)两端逐渐施加一轴向拉伸载荷,使之发生变形直至断裂,便可得到试样伸长率(试样原始标距的伸长与原始标距之比的百分率)随应力(试验期间任一时刻的力除以试样原始横截面积之商)变化的关系曲线,称为应力-应变曲线,图1-6所示为低碳钢的应力-应变曲线。

图1-5 圆形标准拉伸试样

图1-6 低碳钢的应力-应变曲线
在应力-应变曲线中,OA段为弹性变形阶段,此时卸掉载荷,试样恢复到原来尺寸。A点所对应的应力为材料承受最大弹性变形时的应力,称为弹性极限。其中,OA′部分为一斜直线,应力与应变呈比例关系,A′点所对应的应力为保持这种比例关系的最大应力,称为比例极限。由于大多数材料的A点和A′点几乎重合在一起,一般不作区分。
在弹性变形范围内,应力与伸长率的比值称为弹性模量E。E实际上是OA线段的斜率,E=tanα(MPa),其物理意义是,产生单位弹性变形时所需应力的大小。弹性模量是材料最稳定的性质之一,它的大小主要取决于材料的本性,除随温度升高而逐渐降低外,其他强化材料的手段(如热处理、冷热加工、合金化等)对弹性模量的影响很小。材料受力时抵抗弹性变形的能力称为刚度,其指标即为弹性模量。可以通过增加横截面积或改变截面形状来提高零件的刚度。
1)强度
材料的强度是指材料在外力作用下抵抗破坏的能力,它是衡量材料变形抗力和断裂抗力的性能指标。从本质上来说,材料的强度应是其内部质点间结合力的表现。材料受外力作用时,在其内部便产生应力,此应力随外力的增大而增大,当应力增大到材料内部质点间结合力所能承受的极限时,应力再增加便会导致内部质点的断开,此极限应力值就是材料的极限强度,通常简称为强度。根据加载方式不同,强度指标有许多种,如抗拉强度、抗压强度、抗弯强度、抗剪强度、抗扭强度等。其中,以拉伸试验测得的屈服强度和抗拉强度两个指标应用最多。
(1)屈服强度。在图1-6中,应力超过B点后,材料将发生塑性变形。在BC段,塑性变形发生而力不增加,这种现象称为屈服。B点所对应的应力称为屈服强度(σS)。屈服强度反映材料抵抗永久变形的能力,是最重要的零件设计指标之一。实际上多数材料的屈服强度不是很明显,因此,规定拉伸时产生0.2%残余延伸率所对应的应力为规定残余延伸强度,记为σ0.2,如图1-7所示。

图1-7 条件屈服强度的确定
(2)抗拉强度。图1-6中的CD段为均匀塑性变形阶段。在这一阶段,应力随应变增加而增加,产生应变强化。变形超过D点后,试样开始发生局部塑性变形,即出现颈缩,随应变增加,应力明显下降,并迅速在E点断裂。D点所对应的应力为材料断裂前所承受的最大应力,称为抗拉强度σb。抗拉强度反映材料抵抗断裂破坏的能力,也是零件设计和评价材料的重要指标。
2)塑性
塑性是指金属材料在外力的作用下,产生永久变形(塑性变形)而不被破坏的能力。金属材料在受到拉伸时,长度和横截面积都要发生变化,因此,金属的塑性可以用长度的伸长(延伸率)和断面的收缩(断面收缩率)两个指标来衡量。
金属材料的延伸率和断面收缩率越大,表示该材料的塑性越好,即材料能承受较大的塑性变形而不破坏。一般把延伸率大于5%的金属材料称为塑性材料(如低碳钢等),而把延伸率小于5%的金属材料称为脆性材料(如灰口铸铁等)。塑性好的材料能在较大的宏观范围内产生塑性变形,并在塑性变形的同时使金属材料因塑性变形而强化,从而提高材料的强度,保证零件的安全使用。此外,塑性好的材料可以顺利地进行某些成型工艺加工,如冲压、冷弯、冷拔、校直等。因此,选择金属材料做机械零件时,必须满足一定的塑性指标。
(1)伸长率δ:
式中 l1——拉伸后的长度(mm);
l0——原长度(mm)。
(2)断面收缩率ψ:
式中F1——断口处横截面积(mm2);
F0——原横截面积(mm2)。
由于δ值与试样尺寸有关,一般规定l0=5d0(短试样)或l0=10d0(长试样),分别以δ5或δ10表示伸长率,δ10通常写成δ。
一般δ达5%,ψ达10%能满足大多数零件要求。
评价冷作模具材料塑性变形抗力的性能指标主要是常温下的屈服点σs;评价热作模具材料塑性变形抗力的指标为高温屈服点或高温屈服强度。当模具的工作应力超过模具材料的相应屈服点时,模具就会产生过量塑性变形而失效。
反映冷作模具材料的断裂抗力的性能指标是室温下的抗拉强度σ b、抗压强度和抗弯强度等。反映热作模具材料的断裂抗力的性能指标除了抗拉强度等之外,还包括断裂韧度(即反映裂纹扩展的抗力指标),因为大多数热作模具的断裂属于表面热疲劳裂纹扩展所造成的断裂。(1-2)
4.韧性
韧性是材料在冲击载荷作用下抵抗产生裂纹的一种特性,反映了模具的脆断抗力,常用冲击韧度αk来评定。αk越大,材料的韧性越好,在受到冲击时越不易断裂。冲击韧度反应了材料抵抗冲击载荷的能力。
αk=Ak/S(J/cm2) (1-3)
式中 Ak——冲击功,摆锤冲断试样所失去的能量,即对试样断裂所做的功(J);
S——试样缺口处截面积(cm2)。
在如图1-8所示的摆锤式冲击试验机上用规定高度的摆锤对处于简支梁状态的缺口试样进行一次冲断,可测得冲击吸收功Ak。试验所用冲击试样根据其缺口形状分为U形缺口冲击试样和V形缺口冲击试样两种,如图1-9所示,测得的冲击韧度分别用αku、αkv表示。
冷作模具材料因多在高硬度状态下使用,在此状态下αk值很小,很难相互比较,因而常根据静弯曲挠度的大小来比较其韧性的高低。工作时承受巨大冲击载荷的模具,须把冲击韧度作为一项重要的性能指标。
影响强度和韧性的主要因素有材料的化学成分、冶金质量、晶粒大小、组织类型,碳化物的形状、数量、大小及分布。所以,根据模具的工作条件和性能要求,合理地选择模具钢的化学成分、组织状态及热处理工艺,就能够得到最佳的强韧性配合。
5.疲劳抗力
疲劳抗力是反映材料在交变载荷作用下抵抗疲劳破坏的性能指标。根据不同的应用场合,有疲劳强度和小能量多冲抗力等。对于热作模具,大多数在急冷急热条件下工作,必然发生不同程度的冷热疲劳,因此,还要把冷热疲劳抗力作为热作模具材料的一项重要性能指标。

图1-8 摆锤式冲击试验机示意图

图1-9 标准缺口冲击试样
疲劳失效与静载荷下的失效不同,断裂前没有明显的塑性变形,发生断裂比较突然。实际服役的金属材料有90%是因为疲劳而破坏。疲劳破坏是脆性破坏,它的一个重要特点是具有突发性,因而更具灾难性。
疲劳产生的原因是,机构上的每一点都承受交变载荷的作用,如果某一点有一小裂纹,在拉应力的作用下,裂纹扩展,在压应力的作用下,裂纹闭合,在交变载荷的作用下,裂纹不断被拉开和闭合,当裂纹扩展到一定程度时,机构的有效承载面积无法承受外加载荷的作用,发生突然断裂。由此可见,疲劳断裂是由疲劳裂纹产生-扩展-瞬时断裂三个阶段组成的。因此,疲劳断口一般以疲劳裂纹源为中心,逐渐向内扩展形成海滩条纹的裂纹扩展区和呈纤维状的瞬时断裂区。
材料承受的交变应力σ 与断裂时应力循环次数N之间的关系可用疲劳曲线来描述(见图1-10)。随着σ 的下降,N值增加,材料经无数次应力循环后仍不发生断裂时的最大应力称为疲劳极限。对称循环交变应力的疲劳极限用σ-1表示。在实际当中,做无限次应力循环的疲劳试验是不可能的,对于钢铁材料,一般规定疲劳极限对应的应力循环次数为107,有色金属为108。
提高疲劳极限的途径:
(1)在零件结构设计中尽量避免尖角、缺口和截面突变,以免产生应力集中,从而产生疲劳裂纹。
(2)提高零件表面加工质量,减少疲劳源。
(3)采用各种表面强化处理。

图1-10 疲劳曲线示意图
1.2.3 模具材料的选用原则
一般来说,应根据模具加工能力和模具的服役条件,结合模具材料的性能和其他因素,来选择符合要求的模具材料。对于某一种类的模具,很多材料从基本性能上看都能符合要求,然而必须根据所制成模具的使用寿命、生产率、模具制造工艺的难易程度及成本高低来作出综合评价,这就必须同时考虑模具材料的使用性能、工艺性能和生产成本等因素。
1.模具材料的使用性能
各种模具的服役条件不同,对模具材料的性能要求也不相同。模具工作者常要根据模具的服役条件和使用寿命要求,合理地选用模具材料及热处理工艺,使之达到主要性能最优,而其他性能损失最小的最佳状态。对各类模具材料提出的使用性能要求主要包括硬度、强度、塑性、韧性等。
2.模具材料的工艺性能
在模具生产成本中,材料费用只占15%左右,而机械加工、热处理、装配和管理等费用占80%以上。所以,模具材料的工艺性能就成为影响模具生产成本和制造难易的主要因素之一。模具材料的工艺性能主要有如下几种:
(1)可加工性。钢材的可加工性主要包括切削、磨削、抛光、冷拔等加工性和锻压加工性等。模具钢大多属于过共析钢和莱氏体钢,热加工性能和冷加工性能都不太好,必须严格控制热加工和冷加工的工艺参数。近年来为改善钢的切削加工性,在钢中加入易切削元素或改变钢中夹杂物的分布状态,从而提高模具表面质量和减少刀具的磨损。
随着电子技术的发展,数控机床和加工中心乃至计算机控制技术的广泛运用,模具钢除应具有良好的切削加工性外,还要有良好的镜面抛光性能、电加工性能及压印翻模加工性能等。
(2)淬硬性和淬透性。淬硬性主要取决于钢的碳含量,淬透性主要取决于钢的化学成分和淬火前钢的原始组织。模具对这两种性能的要求根据其服役条件不同各有侧重,对于要求整个截面有均匀一致性能的模具,如热作模具、塑料模具,则高的淬透性显得更重要些;而对于只要求有高硬度的小型冷作模具,如冲裁落料模具,则更偏重于高的淬硬性。
(3)淬火温度和热处理变形。为了便于生产,要求模具钢的淬火温度范围尽可能宽些,特别是当模具采用火焰加热局部淬火时,要求模具钢有更宽的淬火温度范围。除部分采用预硬型钢制作的模具外,绝大多数模具是在切削加工后,通过热处理而获得所需的组织和性能。因此,要求淬火时尺寸变化小,各向具有相近似的变化,且组织稳定。
(4)脱碳敏感性。模具钢在锻造、退火或淬火时,若在无保护气氛下加热,其表面层会产生脱碳等缺陷,而使模具的耐用度下降。脱碳敏感性主要取决于钢的化学成分,特别是碳含量。在钢中Wsi=0.8%~1.0%,会加剧脱碳。
1.2.4 模具材料的生产现状和发展趋势
随着工业生产技术的发展和新材料的不断出现,模具的工作条件日益苛刻,对模具材料的性能、质量、品种等方面也不断提出了更高、更新的要求。为了适应这些要求,世界各国近年来都积极地开发了具有各种特性、适应不同要求的新型模具材料。
从我国1985年制定的国家标准GBl299/T—1985中的钢号来看,钢种系列比较完整,既包括了国内外通用的性能较好的模具钢,也纳入了一些国内研制的新钢种,基本上可以满足模具制造业的需要。但是在钢种系列、产品结构和应用方面还存在着一些问题,主要问题如下:
(1)钢种系列有待进一步完善,如用量很大的塑料模具钢,在GB/T1299—1985中只纳入了3Cr2Mo一个钢号,这显然不能满足各种不同塑料模具的要求。
(2)钢种产品结构和选用很不合理,如塑料模具产量很大,但目前很大数量的塑料模具是采用45钢制造的,模具的使用寿命很低,生产的塑料制品质量不高。
冷作模具钢的钢号系列比较完整,但目前占产量70%左右的是Cr12、Crl2MoV、CrWMn三个钢号。世界上用量较大、综合性能较好的CrSMolV钢,虽已纳入国家标准,但产量很少;耐磨性较好的Crl2Mo1V1钢,用量也不大。
热作模具钢的产品结构要好一些,通过10余年的大力推广,世界上应用最广、综合性能较好的中合金铬系热作模具钢4CrSMoSiVl的产量已居热作模具钢的首位。传统的热作模具钢3Cr2W8V,其抗冷热疲劳性能和韧性较低,生产成本高,在有的国家标准钢号中已被淘汰,但是国内的产量仍较高,年产量仍在1万吨以上,还需要进一步做工作。
1.塑料模具钢
20世纪50年代以来,世界塑料工业迅速发展,塑料已经成为一种重要的工业材料。塑料制品大部分采用模压成形,不少工业发达国家塑料模具的产值已经居模具产值的第一位。塑料模具钢已逐渐发展成为一个专用钢材系列。
我国的专用塑料模具钢还没有形成系列,纳入GB/T1299—1985的只有3Cr2Mo一个钢号,常选用碳素钢,加工成形后不经热处理就交付使用,因而模具表面粗糙度值较高,图案花纹容易磨损,加工出来的塑料制品外观质量很差。而精密塑料模具常采用合金工具钢制造,机械加工性能差,热处理变形问题更是无法解决。因此,直到目前为止,关键部件的塑料模具材料还依赖于进口,造成模具成本高,外汇流失严重。鉴于此问题,国内有关科研院所和大专院校对塑料模具专用钢进行了研制,并取得了一些进展。
我国近年研制的塑料模具钢主要有P20BSCa、P20SRe、FT、OCr4NiMoV(LJ)、TG2、25CrNi3MoAl、10Ni3MnCuAIMo(PMS)、OCrl6Ni4Cu3Nb(PCR)、06Ni6CrMoVTiAI、空冷12、Y82、Y55CrNiMnMoV(SM1)、Y20CrNi3AlMnMo(SM2)钢等。
2.冷作模具钢
冷作模具是应用范围最广的模具,冷作模具的产值历来居模具制造业的首位,近年来由于塑料模具的迅速发展,在不少工业发达国家已退居模具工业产值的第二位。目前通用的冷作模具钢可分为三大类:
(1)低合金冷作模具钢。以CrWMn和9Mn2V为代表,耐磨性和热硬性较差,而韧性较高,一般可采用油淬火,成本较低,广泛用于生产批量不大的冷作模具。
(2)中合金冷作模具钢。以Cr5MolV为代表,具有中等的耐磨性和热硬性,韧性也较高,淬透性好,可以空淬,综合性能好,广泛用于生产中等批量产品的冷作模具。
(3)高碳、高铬型冷作模具钢。以Crl2MolVl和Crl2钢为代表,耐磨性和热硬性较高,由于含有大量的共晶碳化物,所以韧性较差,广泛用于生产批量较大,要求耐磨性很高但冲击载荷较小的冷作模具。
近年来发展的新型冷作模具钢主要有9Cr6W3Mo2V2(GM)、6CrNiSiMnMoV(GD)、7CrSiMnMoV、8Cr2MnWMoVS(8Cr2S)、5Cr4Mo3SiMnVAl(012Al)、6Cr4Mo3Ni2WV(CG-2)、7Cr7Mo2V2Si(LD)、Cr8MoWV3Si(ERS)等。
3.热作模具钢
热作模具钢主要用于制造金属材料热加工用的模具,用量最大的为三类通用型热作模具钢。
(1)低合金热作模具钢。代表性钢号为5CrMnMo和5CrNiMo等,这类钢有较好的淬透性和冲击韧度,但热硬性不够,一般用于股役温度不高而冲击载荷较大的模具,如锤锻模等。
(2)中合金热作模具钢。这类钢为铬系热作模具钢,代表性钢号有4Cr5MoSiVI(H13)、4Cr5MoSiv(H11)、4Cr5MoWSiv(H12)、4Cr3M03Siv(H10)等。这类钢有良好的综合力学性能、高的热强性、抗冷热疲劳性能及抗液态金属冲蚀性,已经广泛用于锻压模具、铝合金压铸模具和热挤压用模具,成为当前应用最广的一类热作模具钢。
(3)高合金热作模具钢。应用最广的是传统的钨系热作模具钢,如3Cr2W8V等。用于工作温度较高的模具,近年来大部分已被中合金热作模具钢取代。
为了适应一些热作模具的特殊要求,开发了一些新型高性能热作模具钢,主要有4Cr3Mo3W4VNb、4Cr3Mo2MnVNbB(Y4)、4CrSMo2MnVSi(Y10)、3Cr3Mo3VNb(HM3)、4SiMnW3Mo2VNb、9Mn9Ni4Cr8V2WMo、5Mnl5Cr8Ni5Mo3V2、4Cr3Mo2 NiVNbB(HD)、2Cr3Mo2NiVSi(PH)钢等。
提高模具钢的内在质量主要包括两个方面。
(1)提高模具钢的纯净度。降低钢中有害杂质和气体的含量,提高钢的纯净度,是当前各模具钢生产厂的主要努力方向之一。
如将4Cr5MoSiVl钢中磷的质量分数从0.03%降至0.01%,可使其淬火回火后的冲击韧度提高1倍;如果进一步降至0.001%,则可提高冲击韧度2倍。将钢中的氧含量降低,也可以显著改善钢的韧性。
(2)提高钢的等向性。模具大部分是多向受力的,因此,提高模具钢的等向性,改善钢的横向韧性和塑性,使其与纵向性能接近,就可以大幅度提高模具的使用寿命。