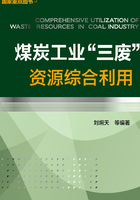
1.6 循环流化床燃烧污染物生成与控制
1.6.1 燃烧中脱硫
循环流化床燃烧过程中添加合适粒度的石灰石等脱硫剂,可以实现燃烧过程中的脱硫,是一种低成本控制SO2排放的技术,这也是循环流化床燃烧的优势之一。
(1)炉内脱硫过程
循环流化床燃烧中,煤的硫分在燃烧室内反应生成SO2及其他的一些含硫物质,同时,具有一定粒度分布的石灰石被给入燃烧室,这些石灰石被迅速地加热,发生煅烧反应,产生多孔疏松的CaO。SO2扩散到CaO的表面和内孔,在有氧气参与的情况下,CaO吸收SO2并生成CaSO4。生成的CaSO4逐渐地把空隙堵塞,并不断地覆盖新鲜CaO表面,当所有的新鲜表面都被覆盖后反应就停止了。这一过程的示意见图1-23。当然脱硫剂颗粒也可能在还未达到上述状态时就被吹出了燃烧室,这时对脱硫剂颗粒的利用显然是不充分的[24]。

图1-23 常压循环流化床中石灰石脱硫过程示意
脱硫过程本质上是一系列的气固反应,具体的脱硫效果由各个反应进行的情况决定。投入燃烧室的石灰石首先发生煅烧反应:
煅烧反应是脱硫反应的前期准备,这时产生的大量孔隙极大地增加了脱硫颗粒的可用表面积。煅烧反应进行的情况直接影响生成孔隙的大小及其分布、CaO颗粒的比表面积以及CaO晶粒的大小等,进而直接影响CaO颗粒脱硫反应的特性。影响这些参数的主要因素有煅烧温度、环境CO2浓度和石灰石本身的特性等。大部分石灰石的煅烧温度在850℃左右;当温度上升到920℃时,普遍发生烧结,煅烧产物的比表面积严重下降,因此床温应该控制在850℃左右。
在有氧气存在的条件下与SO2接触时,会发生:
这是一个总包反应方程,其具体的反应途径尚不清楚。
(2)脱硫反应影响因素
CaSO4分子体积远大于CaO,因而当SO2扩散到CaO内表面发生反应时,生成的产物会把微孔堵死,使得可用的内表面积减小。微孔越是深入到颗粒内部,则其被堵塞而不能被充分利用的可能性越大。事实上,电子探针实验表明,石灰石的转化仅限于表面以内的数十微米[25]。对于小颗粒,由于它的比表面积要比大颗粒大,而且孔隙更接近表面,因而实验中观察到小颗粒的最大转化率要比大颗粒高。但是在具体的脱硫过程中,由于颗粒可能在达到最大转化率之前被吹出锅炉,因而各粒径石灰石的实际转化率的分析是非常复杂的。
石灰石的特性主要包括它的物理特性和化学特性。物理特性主要包括石灰石煅烧后生成孔隙的大小、分布及比表面积等。对脱硫反应而言,直径大于0.03μm的孔隙才是比较重要的,更细的孔隙产生的扩散阻力很大,不利于脱硫反应的进行,而且微孔很容易被CaSO4堵塞致使其表面积利用率很低,因此要使煅烧产物的孔隙分布较为合理、比表面积较大,所使用的石灰石物理特性是很重要的。前面已经提到,石灰石的转化仅限于表面以内的几十个微米。反应主要是在表面进行的,总表面积取决于颗粒的大小,这就要求颗粒直径尽量小;但是考虑到在达到最大转化率之前被烟气携带离开主循环回路,颗粒粒度也不能太小,最佳范围在150~200μm。
化学特性的影响主要指石灰石所含杂质的影响。已经发现许多杂质的存在会对石灰石的转化率产生影响。杂质的存在会使CaO颗粒在固硫过程中孔隙被堵塞的时间推迟,因而可以提高CaO颗粒的利用率。
由于循环流化床底部的密相区处于氧化/还原气氛的不断更迭状态之中,在氧化性气氛下,趋于生成CaSO4;在还原性气氛下,最稳定的则是CaS,在循环流化床的底渣中常可测到少量的CaS;两者中间有一个过渡区,这里最稳定的是CaO。在实际的循环流化床中,密相区的CaSO4在床温高于850℃下加速分解,会释放出已经被捕集的SO2。
无论是在较小的实验台上还是在大型的循环流化床上,都发现当床温处于850℃左右时脱硫效率最高,见图1-24,这是由于床温低于850℃时,煅烧反应的速率明显下降,石灰石煅烧产生CaO的速率限制了脱硫反应的进行,因而使脱硫效率较低。当床温高于850℃时,CaO内部孔隙结构发生烧结而减弱了CaO与SO2反应的活性,于是导致脱硫效率下降;还有学者认为此时脱硫产物CaSO4在还原性气氛中分解速率增加较快,导致已经被捕集的SO2重新被释放出来,因而脱硫效率下降。目前后一种理论得到了更加广泛的支持。

图1-24 温度对脱硫效率的影响
(3)石灰石脱硫钙硫比
循环流化床的一个重要优势是燃烧过程中利用石灰石等作为脱硫剂脱硫。原煤中的各项成分,在加入了脱硫剂之后要发生变化,计算时必须用折算值而不是原始值。
一般常用的脱硫剂是石灰石(CaCO3)、白云石(CaCO3·MgCO3)等。石灰石和白云石等吸收SO2的能力是有一定限度的,反应过的脱硫剂要不断排出,新的脱硫剂要不断被加入。向流化床中加入的脱硫剂量,要根据煤中的含硫量进行计算,保证能够达到一定的脱硫效率以满足环境保护标准的要求。在循环流化床中,石灰石中的钙能否有效地被用来脱硫,取决于石灰石本身的反应性、循环流化床的运行条件等。一般情况下,850~900℃是脱硫的最佳反应温度,随煤种的不同有所变化,这也是循环流化床选择850~900℃作为运行温度的原因。为了确定达到一定的脱硫效率所需要的CaCO3量,常用钙硫的摩尔比值Ca/S作为一个综合指标,用来说明在脱硫时钙的有效利用率。对于运行正常的循环流化床锅炉,可以根据收到基的硫含量和脱硫效率的要求,用图1-25估计870℃条件下所需要的Ca/S值[20]。为达到一定的脱硫效率所需的Ca/S值越高,钙利用率则越低。

图1-2 5 Ca/S确定方法
循环流化床锅炉石灰石脱硫过程中,由于煅烧吸热、固硫放热、增加灰渣物理热损失,因此会影响到锅炉效率,其影响与Ca/S值有关。一般说来,在Ca/S值低于2.5时,脱硫会改善锅炉效率,在Ca/S值大于2.5时,脱硫会降低锅炉效率。
实践表明,循环流化床锅炉具有很强的炉内脱硫能力,对于多种不同燃料,燃料的含硫量从0.3%到8.0%,循环流化床锅炉均能达到96%以上的脱硫效率,最高脱硫效率甚至可以达到99.5%,最低SO2排放值为18mg·m-3。表1-7为我国实际运行的部分循环流化床锅炉的实际脱硫效率。
表1-7 我国典型循环流化床锅炉的实际脱硫效率

循环流化床锅炉的脱硫优势已经得到国际上的公认,但是在我国由于各种历史原因,石灰石系统没有建设或者建设了但运行不正常,脱硫效果不佳甚至没有脱硫,这都曾经一度引起环保部门对循环流化床锅炉的脱硫产生极大的怀疑。近年来环保标准更加严格、执行力度更强,新建设的大容量循环流化床锅炉发电机组,脱硫系统比较完善、运行规范,循环流化床锅炉的脱硫优势逐渐得到充分发挥,很多机组的实际脱硫效率达到了90%以上,有的甚至在较低的Ca/S值(1.7)条件下,能够达到94%左右的脱硫效率。在控制床温在不超过870℃左右、合理控制石灰石粒度分布、选择反应活性较高的石灰石、石灰石的连续稳定供给条件下,只要保证一定的Ca/S值,脱硫效率是比较高的。图1-26是某300MW循环流化床锅炉的SO2排放实时监测结果。

图1-26 某300MW循环流化床锅炉烟气SO2浓度曲线
当然,最终排放浓度与燃料的原始含硫量有关。目前我国的循环流化床锅炉的燃料没有选择的空间,基本上是劣质燃料,折算硫分一般较高,这就对床温、粒度、石灰石种类、石灰石系统的稳定性、Ca/S值等的运行控制和管理的要求更加严格。
尽管循环流化床的脱硫效率很高,但在某些条件下,对SO2的排放要求更高,此时需要采用二级烟气处理系统,以进一步降低SO2的排放,同时提高石灰石的利用率,使得在脱硫的同时还可以脱除酸性气体和重金属[26]。
1.6.2 氮氧化物生成与控制
固体燃料燃烧过程中产生的氮氧化物主要是一氧化氮(NO)和二氧化氮(NO2),此外,在低温燃烧下会有氧化亚氮(N2O)产生。
氮氧化物在燃烧过程中的生成和排放浓度与煤燃烧条件之间的关系密切,如煤的燃烧方式、燃烧温度、过量空气系数等。固体燃料在循环流化床燃烧生成的NO占总NOx的90%以上,NO2占5%~10%,N2O占1%左右。燃烧过程中NOx的生成途径分别是空气中的氮气在高温下氧化而生成的热力型NOx、燃料氮氧化生成的燃料型NOx、空气中的氮生成的瞬时反应型NOx。燃烧温度低于1300℃时,几乎观测不到高温型NOx的生成反应;瞬时反应型NOx产生于燃烧时CHi类离子团较多、氧气浓度相对低的富燃料燃烧情况。因此,循环流化床燃烧中氮氧化物的生成与控制的重点是燃料型NOx。
由于一般燃烧温度较高的常规燃烧设备中N2O的排放浓度很低,过去对由化石燃料燃烧生成的N2O对大气环境的破坏重视不足。近年来,随着流化床燃烧技术的迅速发展和循环流化床的大量应用,人们开始注意到燃煤循环流化床N2O的排放问题。N2O不仅能破坏大气同温层的臭氧层,而且它还是一种温室效应气体。N2O在大气对流层相当稳定,存活期达150年以上,因此它不会像NOx那样会由降雨而返回地面,形成对流层的氮循环。
煤炭中的氮含量一般在0.5%~2.5%,它们是以氮原子的状态与各种碳氢化合物结合成氮的环状化合物。煤中氮的有机化合物C—N的结合键能比空气中的氮分子的键能小得多,因此氧更容易首先破坏C—N键而与氮原子生成NO。煤燃烧时75%~90%的NOx是燃料型NOx,因此,它是燃烧产生NOx的主要来源[7]。
燃料型NOx的生成机理非常复杂,虽然多年来世界各国许多学者为了弄清楚其生成和破坏的机理,进行了大量的理论和实验研究工作,但到现在对这一问题仍然没有完全弄清楚。这是因为燃料型NOx的生成和破坏过程不仅与煤种特性、煤的结构、燃料中的氮热分解后在挥发分和焦炭中的比例、成分和分布有关,而且大量的反应过程还与燃烧条件,如温度和氧及各种成分的浓度等关系密切。
一般的燃烧条件下,燃料中含氮有机化合物首先被热分解成HCN和NH3等中间产物,随挥发分一起从燃料中析出,称为挥发分N。挥发分N析出后,残留在焦炭中的氮称为焦炭N,见图1-27。焦炭N的析出情况比较复杂,与氮在焦炭中N—C、N—H之间的结合状态有关。由于焦炭N生成NO的反应活化能比碳燃烧的反应活化能大,因此焦炭NOx是在焦炭燃烧区后部生成。高温条件下,由焦炭N所生成的NOx占总NOx生成量的25%~30%。在循环流化床燃烧条件下,由于焦炭的燃尽本身就比较难,因此焦炭N转化为NOx的极少,几乎可以忽略。煤被加热挥发分析出量达到一定数量时,挥发分N才开始析出。燃料N转化为挥发分N和焦炭N的比例与煤种、热解温度及加热速率等有关。对于高挥发分煤种,热解温度和加热速率提高时,挥发分N产率增加,而焦炭N相应地减少。过量空气系数α对挥发分N的产率没有影响[6]。

图1-27 煤中的氮分解为挥发分N和焦炭N示意
挥发分N中最主要的氮化合物是HCN和NH3,其所占比例不仅取决于煤种及其挥发分的性质,而且还与温度等有关。对烟煤来说,HCN在挥发分中的比例比NH3大;劣质煤的挥发分N中则以NH3为主;无烟煤的挥发分N中HCN和NH3相当。挥发分中HCN和NH3的产率随温度的增加而增加,但在温度超过1100℃时,NH3的含量达到饱和。随着温度的上升,燃料N转化为HCN的比例大于转化成NH3的比例。
挥发分N中HCN被氧化的主要反应途径如图1-28所示。随挥发分一起析出的挥发分N在挥发分燃烧过程中,遇到氧会发生一系列均相反应,其N中的HCN氧化生成NCO后可能有两种反应途径,这取决于NCO生成后所遇到的反应条件。在氧化性气氛中,NCO会进一步氧化成NO;若遇到还原性气氛,则NCO会反应生成NH。生成的NH在氧化气氛中会进一步被氧化成NO,成为NO的生成源;同时NH在还原气氛中又能与已经生成的NO进行氧化、还原反应,使NO被还原成N2,成为NO的还原剂。

图1-28 挥发分N中HCN被氧化的主要反应途径
挥发分N中NH3被氧化的主要反应途径如图1-29所示。可见NH3在不同条件下,可能作为NO的生成源,也可能成为NO的还原剂。

图1-29 挥发分N中NH3被氧化的主要反应途径
流化床燃烧时由挥发分N生成的NOx占燃料型NOx的70%~75%。在氧化气氛中,过量空气系数增加时,挥发分N生成的NOx迅速增加。
由于挥发分N的氧化对NOx的生成有重要影响,因此挥发分含量的大小直接影响NOx生成量,见图1-30。燃料N的增加,会明显提高NOx排放。

图1-30 挥发分含量对NOx生成的影响
由HCN和NH3的演化途径可知,在氧化气氛中生成的NOx遇到还原性气氛时,会还原成氮分子,这称为NOx的还原或破坏。因此,最初生成的NOx的浓度并不等于其排放的浓度,因为随着燃烧条件的改变,有可能把已经生成的NOx还原成N2而破坏掉。所以燃煤设备烟气中NOx的排放浓度最后取决于NO的生成反应和NO还原或被破坏反应的综合结果。
NOx的破坏途径见图1-31,可见破坏或还原NOx有三条可能的途径。在还原气氛中NO通过烃类(CHi)或碳被还原,见图1-31途径(a),生成HCN,然后HCN与O发生反应,生成中间产物NCO等。在还原气氛中,NCO会生成NHi。此时生成的NHi在还原性气氛中如遇到NO则会将NCO还原为N2。在燃煤火焰中当NO遇到碳时,则有可能被还原成N2和CO、CO2气体。根据这个原理,可将含烃燃料喷入含有NO的燃烧产物中,即燃料分级燃烧技术,可以有效地控制NOx的排放。在还原气氛中,NOx与氨类(NHi)和氮原子(N)反应生成氮分子(N2),如图1-31途径(b)所示。由图1-31可以看出,NO的还原和破坏,是通过NCO和NHi的反应而实现的。同时,通过NCO和NHi还可以由图1-31途径(c)通过NO的破坏而生成N2O。由此可见,N2O的生成源是NO。

图1-31 NOx破坏的反应途径
循环流化床锅炉中,燃烧是在分级燃烧过程中实现的;下部密相区中,燃料颗粒位于空气非常少的乳化相中,没有充分的氧气供给,处于富氧条件下的欠氧燃烧状态;炉膛上部稀相区中心普遍存在氧气浓度近于0的贫氧区,因此炉膛整体上的燃烧是还原性气氛[10],炉膛出口的CO含量很高,在分离器中继续燃烧。同时,由于燃烧的需要,主循环回路中有大量的焦炭,主循环回路中的焦炭含量与燃料的反应活性有关。对于无烟煤、石油焦、贫煤等难燃燃料,由于反应活性低,燃烧反应速率慢,因此需要更多的反应表面,物料中的碳含量较高;而褐煤等高反应活性的床料含碳量较低。因此,循环流化床锅炉的NOx排放随着燃料挥发分的增加而提高,与煤粉燃烧呈现了相反的规律,见图1-30(b),因为煤粉燃烧的NOx还原主要依赖于挥发分。燃烧的还原性气氛以及主循环回路存在的大量焦炭颗粒,利于生成的NOx还原,因此NOx生成很少。表1-8为我国实际运行的部分循环流化床锅炉的实际NOx排放。图1-32为某300MW循环流化床锅炉实际运行的NOx浓度检测结果。
表1-8 我国典型循环流化床锅炉的实际NOx排放浓度


图1-32 某300MW循环流化床锅炉烟气NOx浓度曲线
对于NOx低于200mg·m-3的要求,绝大部分循环流化床锅炉能够满足;但是如果进一步要求NOx低于100mg·m-3,就需要考虑燃料、床温、过量空气系数等对NOx的显著影响。无烟煤、石油焦、贫煤和低挥发分烟煤条件下,基本可以满足,但是床温不能高于900℃;而对于高挥发分燃料,在床温比较低(<870℃)、燃料N含量比较低(<0.7%)的条件下,基本上可以达到;若床温控制不严,则NOx原始排放超过国标的要求,需要考虑烟气脱硝。
比较经济的方法是采用非催化选择性还原(SNCR),即在锅炉合适的位置上喷入适当的氨气、氨水或者尿素溶液等脱硝剂,发生还原反应:
SNCR的温度窗口比较窄,但循环流化床锅炉分离器以及转向室中的温度都位于SNCR反应的最佳温度窗口之内,因此烟气在此温度窗口停留时间较长。利用旋风分离器的混合作用,利于进一步提高反应程度,减少氨逃逸。同时,循环流化床锅炉的循环灰是富含多种金属氧化物的多孔介质,是氨与NOx反应的催化剂,并提供有效表面。在合适位置上喷氨,循环流化床循环灰的存在将使这一无外加催化剂的反应具有强烈的选择性催化反应特性,从而可以实现无催化剂消耗的SNCR[27],清华大学的实验表明,NOx的还原效率可轻易达到70%以上,这是煤粉燃烧所无法达到的。对于高挥发分燃料,采用SNCR可满足新国标的要求,但是仍然要严格控制床温以降低原始生成量,减轻氨消耗。
1.6.3 汞排放与控制
汞和其他重金属一样,是煤中的一种微量元素。汞元素以三种形式存在,即单质汞(Hg0)、氧化态汞(Hg2+)、吸附在颗粒上的颗粒态汞(Hg-P)。氧化态汞(Hg2+)亲水性很强,而单质汞(Hg0)基本不溶于水。Hg0和Hg2+都以气相的形式存在,并且很容易被颗粒吸附而形成颗粒汞Hg-P。
在循环流化床燃烧条件下,在主循环回路中烟气始终伴随着固体物料,而固体物料是燃烧或脱硫形成的多孔介质,对单质汞(Hg0)和氧化态汞(Hg2+)均有很强的吸附力,因此,巨大部分Hg在燃烧过程中已经转化为颗粒汞,随着排渣和飞灰离开锅炉。剩余的少量单质汞(Hg0)和氧化态汞(Hg2+),在进入除尘装置后,进一步发生吸附。因此,循环流化床燃烧的汞排放很低,绝大部分微量元素都会被富集在飞灰和底渣中,汞转移到烟气中的比例不足10%。也就是说,循环流化床锅炉的汞排放具有先天的优势,完全能够直接满足国标的要求[6]。