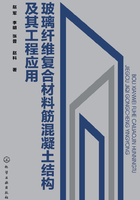
2.2 成型设备
虽然都属于拉挤-缠绕同步方法生产GFRP筋、锚杆,但各种成型设备之间还存在一定的差异。
2.2.1 成型设备分类
按照单方向、双方向缠绕,可以分为单缠绕和双缠绕设备。经常使用的单缠绕设备是指设备可以实现左、右缠绕,以生产出左旋螺纹、右旋螺纹锚杆,用于岩土、煤矿支护使用,旋向与锚杆安装功能有关,对于混凝土使用而言,旋向没有影响。双缠绕设备是指设备有两个独立的缠绕装置,可以同时实现左、右缠绕,由这种方式生产出的GFRP筋材,由于独特的双方向缠绕,导致筋材内部的压力较大,挤胶能力和效果较好,因而筋材纤维含量更高,故强度、模量更高,同时,筋材与混凝土之间的黏结能力更好,这与筋材表面特定的凹凸不平状态有关。
按照最终GFRP筋、锚杆表面是否有缠绕材料,可以分为含缠绕纤维带和不含缠绕纤维带两类产品。美国Hough brother公司生产的Aslan系列GFRP筋,采用表面喷砂和表面螺旋缠绕玻璃纤维束的生产工艺,因而最终GFRP筋含有缠绕纤维带;加拿大Pultraul公司通过研究制造了Isorod GFRP筋,虽然制造过程中使用缠绕材料,但最终GFRP筋表面没有缠绕纤维带。是否含有缠绕纤维带,对GFRP筋、锚杆的力学性能有影响,在2.5节中进行说明。从单方向、双方向缠绕纤维带,并相应利用各自对应的设备生产得到对应筋材角度看,含双方向缠绕纤维带的GFRP筋材、锚杆力学性能更优,但生产难度更大。
按照缠绕材料是否能够循环使用,可以分为循环缠绕丝和缠绕-解缠两种。循环缠绕丝是指将特种钢带作为循环缠绕丝使用,由于此钢带受到热疲劳、力疲劳双重作用,并由于玻璃纤维的摩擦损伤等多种因素,此钢带的使用寿命很短,通常难以超过48h,并且此钢带断裂属于突发事件,事先没有征兆,从而导致生产突然中断、材料浪费等损失。缠绕-解缠是指将缠绕带缠绕在浸渍树脂的玻璃纤维粗纱表面并使其预成型,然后通过热固化成型,再将缠绕带解缠,从而形成GFRP筋材、锚杆表面凹凸不平的状态,加拿大Pultraul公司通过研究制造的Isorod GFRP筋,可能采用此方法。如果换成预先浸渍过树脂的纤维束进行缠绕,则热固化成型后,则不能将缠绕用的纤维带解缠,美国Hough brother公司生产的Aslan系列GFRP筋可能采用此方法。下面重点说明此方法与设备。
2.2.2 循环缠绕丝和缠绕-解缠两种生产设备
两者都属于单方向缠绕,都可生产实心和空心杆体。循环缠绕丝比较适合于大直径GFRP筋的生产,其最小直径难以达到12mm,且肋比较深;而缠绕-解缠可以适应各种直径GFRP筋的生产,其最小直径可以达到4mm,且肋深可以调节。这两种方式都可以生产全螺纹锚杆,故可称为全螺纹锚杆成型机。
采用缠绕-解缠法的全螺纹锚杆成型机由玻纱架、浸胶、缠绕、加热成型、退绕、牵引、切割、下料堆放八部分组成,各部简称为供丝(玻璃纤维)系统、浸胶刮胶系统、缠绕、主体热固化成型系统、退绕系统、牵引系统、切割系统、下料堆放系统。全机采用自动化生产控制过程,一次成型全螺纹锚杆,热固化成型温度可控,生产速度随时可调,生产线可随时停机,随时开机,生产线可连续24h不停机连续运行。工作环境温度为5~35℃,相对湿度为20%~80%。加工的玻璃钢锚杆规格:锚杆长度在800mm以上,锚杆直径为16mm、18mm、20mm、22mm、24mm、25mm、27mm、28mm、30mm、32mm。全螺纹锚杆成型机设备清单见表2-2。
表2-2 缠绕-解缠法的全螺纹锚杆成型机设备清单

采用循环缠绕丝法的全螺纹锚杆成型机与采用缠绕-解缠法的全螺纹锚杆成型机有一定的异同点,两者对比见表2-3。
表2-3 GFRP锚杆生产设备主要工序比较

采用循环缠绕丝法、缠绕-解缠法的全螺纹锚杆成型机不仅可以成型岩土、煤矿支护用GFRP锚杆,其直径在16~32mm之间,还可用于成型同样直径的混凝土用GFRP筋,此两者有一定的差异,表现在锚杆的螺纹精度要求更高,以便于锚杆与螺母的结合,并且煤矿支护需要阻燃、抗静电,因而需要在树脂中添加阻燃剂。对于采用循环缠绕丝法制造的GFRP锚杆,在其外表面另外涂覆抗静电剂,相关内容见第1章的1.4.4“GFRP锚杆表面涂覆抗静电液”部分。对于采用缠绕-解缠法制造的GFRP锚杆,则表面纤维需要在添加有炭黑、阻燃剂的树脂中浸渍,而内部的纤维只需要在添加阻燃剂的树脂中浸渍,这样能够减少由于添加炭黑而导致交联反应速率的下降程度,最终的产品不需要再次涂覆抗静电剂成分等,从此方面看,采用缠绕-解缠法制造的GFRP锚杆更有优势。
采用循环缠绕丝法的一个特别突出的优势在于其树脂用量最少,这会产生正反两方面的效果,减少树脂用量对降低生产成本是有利的,但部分外层的纤维没有树脂的浸渍,出现更多裂纹,会导致力学性能的下降。如果由此生产混凝土增强用GFRP筋,即使采用乙烯基酯树脂,更多裂纹无法抵抗混凝土的强碱性腐蚀,耐混凝土碱性腐蚀的能力会低于采用缠绕-解缠法制造的GFRP筋材。
值得说明的是,锚杆的一个重要指标是抗扭能力,此能力与直径密切相关,根据我国标准MT/T 1061—2008指标要求,锚杆的最小直径是16mm。表2-2描述的是直径在16~32mm之间GFRP锚杆的生产设备组成和功能,以适应较多的玻璃纤维粗纱、不同纤维在不同树脂中的浸渍、相应的生产速度等要求。对于更小直径的GFRP筋材,如ϕ12mm及以下的GFRP筋材,则拟采用更为简洁、高速、灵活的生产设备,由表2-2和表2-3描述的锚杆生产设备生产此类直径更小的筋材,不仅效率低下,甚至不可以生产,下面说明。
GFRP筋的几何尺寸效应明显,即直径越大,筋材强度、模量越小,因而从尽量利用GFRP筋拉伸力学性能角度来看,并且由于黏结强度与直径呈现负相关性的原因,应该多采用小直径的GFRP筋,但表2-2和表2-3描述的锚杆生产设备只是单条生产线,其极限生产速度受到限制,如果能够将同样的功率用于多条生产更小直径的GFRP筋生产线,则总的生产速度提高且能量利用率增加,这就是小直径GFRP筋更多采用多条生产线集中在一套设备的原因,但带来自动化解缠困难而需要人工解缠的问题。
2.2.3 缠绕-解缠方法生产小直径GFRP筋设备
小直径GFRP筋设备基本组成为纱架、导纱板、树脂浸渍槽、预成型模具、缠绕装置、刮胶板、加热固化装置、冷却段、牵引装置和切割装置等,如图2-1所示。

图2-1 缠绕-解缠方法生产小直径GFRP筋设备示意图
(1)纱架 放置生产过程中所需要的纤维增强材料的装置,玻璃纤维纱盘按照要求摆放整齐,纱架壁上开有导纱孔,避免导纱过程中玻璃纤维束的缠绕打结;当多条生产线并排排放时,纱架相应并排排放,避免玻璃纤维束缠绕打结是重点。
(2)导纱板 一方面是将玻璃纤维按束分离,避免玻璃纤维束之间的缠绕打结;另一方面使玻璃纤维束进入浸渍槽时有一定的张力,便于树脂充分浸润。
(3)树脂浸渍槽 保证基体树脂能够更加充分地浸润纤维,其上方装有可拆卸的辊轴,辊轴可以使纤维完全浸没在基体树脂之中,纤维浸胶效果的好坏对筋材的性能影响很大。
(4)预成型模具 将需要生产的筋材直径对应的预成型模具安装在预成型装置中,根据所需要生产筋材的直径确定合适的纤维纱线密度和对应的股数,充分浸渍树脂的连续玻璃纤维纱由松散状态进入到此预成型模具中变成张紧状态,多余的树脂被挤出流回到树脂槽中;对应小直径的GFRP筋材,可以在一条生产线上同时装配多个预成型模具,如通常两个、四个、六个、八个甚至更多,它们之间可以一排、两排甚至三排排列以节约空间,每条生产线同时生产多根GFRP筋材。
(5)缠绕装置 主要由三相异步电动机,摆线针轮减速机和绕线盘组成,绕线盘上装有校力轴和线圈,线圈上有缠绕材料,缠绕材料通过校力轴施加预拉力,从而控制浸渍树脂后的连续玻璃纤维粗纱束表面的螺纹深度和几何尺寸,缠绕装置中的三相异步电动机由变频器控制,从而控制缠绕速度,以得到不同螺距的GFRP筋材(需要与牵引速度配合);缠绕装置与预成型模具数量相对应,即每个预成型模具必须匹配一个缠绕装置,以满足每条生产线同时生产多根GFRP筋材的要求。
(6)刮胶板 刮胶板设置在浸渍树脂后的连续玻璃纤维粗纱进入加热装置入口前、加热装置中间和加热装置后,其主要作用是将筋材表面多余的树脂刮掉,因为表面树脂过多可能在筋材底部形成很多聚集的突起,这些突起的树脂颗粒本身强度很低,如果不处理将严重影响GFRP筋与混凝土的黏结;另外多余的树脂也会掉落到加热装置的底部造成积胶现象,不能保证生产的稳定性和连续性;刮胶板与预成型模具数量相对应,即每个预成型模具必须匹配一组刮胶板。一般而言,筋材直径越小,则每组刮胶板对应的数量越少,通常采用硅橡胶板作为刮胶板材料,这样可以不伤害到玻璃纤维增强材料而能有效刮除树脂。
(7)加热固化装置 加热固化装置有多种型式,其传热方式也不同,有红外线灯管直接加热空气方式,还有电热加热片加热管道、管道再加热空气的方式等,热的空气加热浸渍树脂后的连续玻璃纤维粗纱,使得树脂交联固化,从而形成GFRP筋材。如采用一个整体箱式加热,可以同时对多根小直径的浸渍树脂后的连续玻璃纤维粗纱进行固化,从而形成相应的GFRP筋材,这样可以提高生产速度,每根GFRP筋材只需要配备一个刮胶板;而采用多段管式加热,则每次只能生产一根直径较大的GFRP筋材,且需要配备多个刮胶板。此外,还有其他加热方式,如采用微波加热固化方式,该方式最大的特点是可从树脂内部加热,而不是由外到内的传统加热,因而对大直径GFRP筋固化更有利,但存在微波对人体的危害。相对而言,微波加热属于“冷加热”,微波只加热树脂和玻璃纤维,其能量利用率最高,只要能够防止微波对操作人员的伤害,此种加热方式具有更大的前途。
(8)冷却段 由加热固化装置出来的GFRP筋基本固化,此时GFRP筋中心的温度通常高于200℃,远高于树脂的热变形温度(对不饱和聚酯树脂和乙烯基酯树脂而言,通常为60~80℃;对环氧树脂而言,采用酸酐固化后,通常为100~120℃),因而必须采用冷却方式降低GFRP筋的温度。对于小直径的GFRP筋而言,采用强制空气冷却,在连续运行的过程中,筋材温度逐渐下降,从加热固化装置到牵引机入口,10m的距离可以保证。当直径增大时,可以采用喷射冷水的方式进行强制降温,并辅助采用强制空气冷却。但过高的冷却速率,将导致GFRP筋内外表面温度梯度过大而产生附件内应力,并由此产生裂纹而导致力学性能衰减,GFRP筋力学性能离散性偏大与冷却过程有关。
(9)牵引装置 一方面是提供动力的装置,将固化后的GFRP筋从加热固化装置拉出;另一方面可以通过调节牵引机的速度控制筋材在加热固化装置的停留时间,并与缠绕装置配合,可以生产出不同螺距的GFRP筋材。从生产连续性方面看,有连续性的履带式牵引机、间歇性的夹持式牵引机两种,前者对GFRP筋的压力较大,故容易导致筋材变形,但牵引力大以克服沿途阻力,比较适合大直径的GFRP筋;后者对GFRP筋的压力、牵引力都较小,适合小直径筋材。对于一台牵引机同时牵引出多根GFRP筋材的情况,宜采用履带式牵引机。GFRP筋在进入履带式牵引机前,必须经过充分的冷却,最好使得GFRP筋中心的温度低于热变形温度,这样就可以保证GFRP筋不会被牵引机压变形。
(10)切割装置 有自动定长切割与手动人工切割两种,由于GFRP筋材是连续由牵引机引出,所以切割需要在连续运行的条件下进行。切割时会产生一定量的粉尘和气味,此粉尘中含有碎玻璃纤维、碎树脂等物质,这些物质对人体和环境有危害,一般由粉尘收集装置或粉尘收集系统收集,并辅助喷水系统以降低生产车间的粉尘量。气味主要是未反应完全的苯乙烯单体产生的(对于不饱和聚酯树脂和乙烯基酯树脂而言),此物质有危害,在第1章中的1.1节中有专门的说明。当生产车间有多条生产线同时运行时,产生的粉尘和气味是非常严重的,因而相关的装置、个人的防护与保护是必不可少的,由此产生的职业病是潜在的危害。