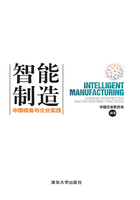
第二节 中国企业智能制造发展阶段判断
基于企业调研,我们认为中国企业智能制造当前总体上处于“广义智能制造的初级阶段”,具体表现在三个方面。
一、从信息化和自动化逐步向智能化过渡
从企业调研发现,由于中国制造业整体仍处于工业2.0、3.0和4.0并行发展期,信息化、自动化和智能化“三化”并存,正处于从信息化、自动化逐步向智能化过渡的阶段,距离狭义智能制造还有较大差距。调研中,几乎所有企业的受访者都提到,信息化和工业化的深度融合是他们工作的起点,也一直是工作重点,而自动化是工业化水平最为重要的表征指标,也是当前企业工业化改造的重点。因此,有不少企业直接将深度信息化和自动化认为是智能化的一部分。其中,企业信息化的主要标志是采用各种信息化硬件设备,在企业管理中采用OA、CRM、ERP等信息化软件,采集的数据主要是生产制造的常规数据。企业的自动化实施则分为三种情况:一是部分辅助环节实现自动化(如内部物料运送),核心环节还没有自动化;二是核心环节基本实现自动化(如自化生产线);三是全流程实现自动化。
实践中,企业的“三化并举”有两种表现方式:一是按顺序逐步推进,即完成了前一步才推进下一步,如太原钢铁就遵循这样的模式。他们提出了五层架构(5L),核心做法是完成ERP、OA、CRM等基础信息化,实现生产数据、试验数据的全自动化(以制造执行系统MES为主要标志),再实现上下游工序的物流、信息流的关联自动化,最后达到生产过程的智能化。另一种是信息化、自动化和智能化同步推进,在有条件的一个或几个工序、工厂中采用自动化或智能化,如株机公司就采用这种模式。他们认为,信息化、自动化、数字化和互联网的结合就是现阶段智能制造的内涵,它在设计环节就包含进用户需求实现了数字化设计,在物流环节、运营环节、质量管理环节和中央控制平台仍然采用信息化和网络化手段。新凤鸣公司也采取了这种同步推进的模式。
二、以智能化的“干中学”为主
由于中国制造业企业从工业2.0向3.0的过渡尚未完成,又遇到了德国工业4.0的新概念,因此学习是当前中国企业开展智能制造的一个显著特征。调研中,几乎所有的企业都提及正在通过不同方式学习,如网上查找资料、购买工业4.0和智能制造书籍、参加培训学习班,甚至远赴德国、美国、日本等实地考察,如株机所生产部负责人就数次前往国外工厂现场参观学习。总体来看,中国企业正处于智能化学习和实践摸索并举阶段,包括概念体系、具体做法、软硬件等的学习,而且这种学习以“干中学”模式为主。大量企业在特定工序、车间或整个工厂中都在探索智能制造的理念和相关模式。
一是概念体系的学习和实践。调研发现,已有不少中国企业对智能制造概念认识有了比较全面的飞跃,如对流程型制造业和离散型制造业的智能化差异有着一致的认识,对信息化、数字化、自动化和智能化之间的关联和区别也有了较深入的思考。因此,中国企业对这一轮智能制造概念的出现保持了相对理性的态度,并没有简单盲从,而是从企业实际角度出发标志智能化的路途。我们在访谈中经常听到企业家讲的最多的一句话就是“我们一直在思考企业是否需要智能制造、如何结合企业实际推进智能制造”,像徐工机械、太原钢铁、镇海炼化、株机公司等企业都有过类似的表述。
二是具体做法的学习和实践。当前,不同国家在智能制造的大框架下有着不同的路径:美国强调发挥互联网在工业4.0中的作用;德国则强调全系统智能化,是“高大上”的代表;日本则强调人与机器智能的协同发展。中国的智能化道路应该怎样走,企业家们正在学习过程中探索。例如,株机所通过学习认识到智能制造的核心是不同流程间的协同,因此专门针对协同问题变革了各环节的衔接,强化人员协同技能的培训提升。中国企业针对智能制造的“干中学”体现在不同层面。大多数企业选择的是特定工序或工厂车间的智能化,只有少数几个企业从全系统的智能化角度进行尝试。
三是对软硬件的学习和实践。不少企业通过对标学习发现,智能制造的重要基础是装备设备的智能化,因此纷纷通过改造现有设备或引入新设备来适应智能制造的需要。例如,蚌埠玻璃院的0.2毫米玻璃生产线装备就是完全由自己研发的,外人难以模仿;株机所也强调高端装备制造的智能化;亨通光电的光纤光缆抽拉丝核心设备也是自主研发的、智能化程度很高的专业设备。还有不少企业将软件系统作为实施智能化的重要手段,这其中包括两类学习。第一类是对购买国外软件系统进行本土化改造,这是一种适应性学习。第二类是对封锁工业软件的自主化设计,这种一种彻底的自力更生和自主创新。例如,株机所在智能化改造过程中,针对设计、工艺、制造的协同需要基于数据库的协同软件支撑,但国外软件很贵并且对方封锁核心代码,逼得株机所开始反向研发、破解软件代码,最终开发出了加强机器间通信协作、提高生产线协同水平的自主工业软件。
三、以增量智能化改造为主
中国制造正处于一种存量智能化和增量智能化并举的阶段,其中存量智能化改造由于转换成本高,而且改造量大,目前还没有大规模开展,增量智能化由于转换成本低,转换风险相对较小,是当前大多数企业推进智能化的重点。我们调研的几乎每家企业都面临制造存量和增量的智能化问题。例如,新凤鸣公司、太原钢铁、株机公司都有老工厂的智能化改造升级问题,究其原因,有些企业是因为老工厂无法快速响应外部顾客要求和生产复杂度的提升(如株机公司),有些是因为老工厂的生产效率相对低下、产品品质不稳定(如太原钢铁),有些是因为人工成本高、生产环境恶劣(如新凤鸣公司)等问题。调研发现,当前中国企业的重点普遍放在增量的智能化方面,因为老企业的智能化改造转换成本过高,新企业则相对简单,买新设备、上马新系统和新软件相对容易实现,即便某些设备和软件并不一定完全适用,仍然可以通过后期的本土化适应性改进来完成。
还需要指出,当前大多数企业对传统存量工厂的改造更多是信息化改造,基于传感器采集自动化数据,按照固定程序操作,机器和设备还不具有自我优化和自主决策的能力,决策仍然主要依靠人工。