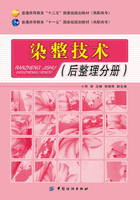
学习任务 2-4 绒面整理
目前,绒布的加工方法很多,除了通过织造的方法直接获得之外,与机械整理加工有关的方法主要有以下几类:
(1) 通过起毛机获得绒布;
(2) 通过磨毛机获得绒布;
(3) 通过割绒方法获得灯芯绒、平绒等;
(4) 通过静电植绒法获得植绒织物;
(5) 纤维发生原纤化获得绒布;
(6) 通过砂洗获得砂洗织物。
此处重点介绍通过起毛机和磨毛机获得绒布的加工方法。
一、起毛整理
古人用植物的荆刺反复刮剐织物表面,使织物中的绒毛被挑出剐起。而现代起绒已经进入设备仪表控制自动化时代,起绒技术应用领域涉及棉、毛、化纤、混纺等原料的机织或针织品,应用范围广。起绒改善了织物外观和风格,使织物表面蓬松厚实,手感柔软,质地丰满,大大提高了织物的服用性能和附加值。
1. 起毛设备 起毛整理是利用起毛的钩刺将纤维末端从纱线中均匀地拉出来,使织物表面产生一层绒毛的加工过程。起毛也称作拉毛或起绒。
刺果起毛机和钢丝起毛机是常见的起毛设备。刺果起毛机作用温和,起绒力小,对织物强力损伤小,但效率低; 钢丝起毛机作用强烈,起绒力大,效率高,但对织物损伤较大。目前,在实际生产中,钢丝起毛机应用较多。
钢丝起毛机的结构主要包括起毛大滚筒、起毛针布辊、除毛屑辊、进出布装置、吸尘装置等(图 2- 20) 。
图 2-20 双动式钢丝起毛机结构示意图
1—张力辊 2—进布辊 3—除毛屑辊 4—出布辊
5—起毛大滚筒 6—针布辊 7—织物
钢丝起毛机是将针布斜向缠绕在滚筒上形成针布辊,若干根针布辊以圆周状平行分布安装在大滚筒的表面,针布辊的数目有 18、24、30、36、40。在钢丝起毛机中,大滚筒、针布辊、织物分别由各自的传动系统拖动,三者的速度可以独立调节、控制。通过调节大滚筒、针布辊、织物三者之间的速度,可以对织物产生起毛或梳理作用。
钢丝起毛机分为单动式(又称单式) 和双动式(又称复式) 钢丝起毛机。单动式钢丝起毛机的针布辊转向一致,钢针弯角方向均相同(图 2-21) 。工作时针布辊自转方向和大滚筒的转向相反,和织物运行方向相同,调节针布辊速度,可以达到不同程度的起毛: 当针布辊速度大于织物速度时产生起毛作用,起毛方向与钩刺弯角方向一致; 起毛作用随着针布辊速度的增加而增加。这种起毛机结构简单,调节幅度小,起毛效果较差,目前较少使用。
双动式钢丝起毛机的起毛大滚筒上装有两组数目相等、钢针钩刺弯角方向相反的针布辊,依次间隔排列。其中钩刺转角与织物运行方向一致的是顺针辊(PR) ,钩刺弯角方向与织物运行方向相反的是逆针辊(CPR) (图 2-22) 。工作时,顺逆针辊自转方向一致,均与织物运行方向和大滚筒转向相反。同样织物、大滚筒、顺逆针辊分别由不同的传动系统拖动,速度可以独立调节,结果使顺(逆) 针辊的钩刺将纤维挑起起毛,而顺(逆) 针辊钩刺则将纤维梳理,如此配合完成起毛过程。
双动式钢丝起毛机起毛效果好,调节范围大,适于多种产品的加工,只是操作复杂,目前被广泛使用。
2. 起毛原理 起毛作用是由针布辊和织物运行的速度差产生的。调节顺逆针辊的速度、大滚筒和织物运行的速度和张力,可以获得不同的起毛效果。
工作时,顺、逆针辊既随大滚筒公转,同时又作与大滚筒方向相反的自转。织物包绕在针布辊表面与大滚筒运行方向一致,且织物运行的速度低于大滚筒表面速度。由于起毛大滚筒、顺针辊、逆针辊和织物的运行速度可以分别独立调节(分别以 VD、VPR、VCPR、VF表示) ,这样通过控制它们之间的速度,使其保持某种关系,即可决定起毛针布辊的起毛作用及效果。
对于逆针辊(CPR) 来说,有三种情况:
①当 VCPR> VD- VF时,逆针辊钩刺插入到织物内部,相对运动导致产生了相对位移,使钩刺再由内部向织物表面移动,并将纤维带出织物表面完成一次起绒过程。其中起绒的强弱取决于VD- VF的差值。差值大,起毛力大,易于损伤织物。
②当 VCPR= VD- VF时,逆针辊与织物相对运动,钩刺插入织物后同步运转又原状从织物中抽出,对织物不产生任何的刮挠作用,无起绒效果,此时称为零点,有柔软、疏松织物的作用。
③当 VCPR< VD- VF时,则钩刺背面与织物接触可将绒毛压向织物一面。当钩刺离开织物表面时,由于有相对运动,可促使钩刺尖部将织物表面绒毛梳理,完成一次梳理过程,具有梳理织物的作用。
同理,顺针辊(PR) 也存在三种状态:
①当 VPR> VD- VF时,有梳理作用。
②当 VPR= VD- VF时,为零点。
③当 VPR< VD- VF时,有起绒作用。
由上述分析可知,通过控制各种速度参数,可以使顺(逆) 针辊起毛或者梳理。在靠近零点时,由于钩刺与织物的相对运动小,起毛和梳理作用减弱; 远离零点时,钩刺与织物的相对运动加大,起毛和梳理作用加强。
3. 影响钢丝起毛机起毛效果的因素和工艺分析
(1) 纺织原料。
①纤维种类: 织物的起毛效果与纤维分子结构和形态、力学性能有直接关系。
棉纤维强度高,适合选用针杆挺壮、尖锐的钩刺或新针布。棉纤维遇到水后起毛困难,所以应先烘干再起毛。另外成熟度好且含一定蜡质的棉,利于起毛。
黏胶纤维与棉结构相近,起毛工艺与棉基本相同。化纤强度大,表面光洁,则选择弹性好、针杆粗、尖锐的针布进行起毛。羊毛强度低,所以选择不锐利的针布起毛。在湿态下起毛对羊毛损伤小。无论是干、湿起毛,对于新针布最好先经过一段时间的棉起毛后,再用于毛织物的
图 2-21 单动式钢丝起毛机工作示意图
1—织物 2—针布辊 3—起毛大滚筒
图 2-22 双动式钢丝起毛机工作示意图
1—织物 2—顺针辊 3—逆针辊 4—起毛大滚筒起毛。
②纤维的细度和长度: 起毛加工主要针对纬纱。通常棉纤维长度越短,线密度越高,起毛后强降小,利于起绒; 反之纤维越长,成纱后纤维间的摩擦力越大,纱线难于解体,起毛困难。
纤维越细,刚性越差,起毛后的弹性差; 线密度相同时,细纤维成纱时纤维根数多,相同捻度下纤维抱合力大,难于起毛。精梳纱使用的纤维较普通纱线长,捻度高,故难起绒。
对于化学纤维而言,粗纤维织物可以获得良好的起毛风格和外观。
总之,从起毛效果、织物强力损伤程度及外观等来看,短纤维织物效果好; 而从风格上看,粗纤维织物效果好。
纤维的细度和长度对产品的强力、风格、外观的影响见表 2-5。
表 2-5 纤维细度、长度对起毛产品强力、风格和外观的影响
③纱的捻度和捻向: 纱线经过加捻,纤维在纱线上的倾角变大,纤维内外缠绕,纱线结构紧密,纤维间摩擦力加大,纱线强度增加,不利于起毛。
若纱线中纤维螺旋排列方向与起毛针布在针布辊包覆缠绕方向一致时,起毛相对较难; 反之起毛容易。
一般来说,Z 捻较 S 捻利于起毛。纬纱是 Z 捻的织物,用逆针辊(CPR) 起毛,起毛效果较好; 纬纱是 S 捻的织物,用顺针辊(PR) 起毛,起毛效果较好。
因此,起毛坯布应含有低度的弱捻纱和纱线纤维捻合比较松散,这样利于起毛。同时要求织物的经纱有足够的强力以保证织物的强度。
(2) 织物组织。
①纬纱密度: 纬密小容易起毛,但绒毛长而稀; 如果纬密过小,纱线容易位移,纬向强度过低。纬密大虽然强力大但出绒少,产生细短绒,绒面效果不好。总之,在保证纬向强力的条件下,纬密尽可能小。
实践证明: 传统双面绒、单面绒产品纬密为 157. 4 根/10cm(40 根/英寸) 时容易起毛,效果也好。为获得细密短绒、强降小的产品,可采用低特(高支) 经纱,并提高经纱密度。仿麂皮绒面织物为了获得绒毛短、密,纬密应选择大些。
②织物组织: 在相同线密度、紧度条件下,起毛难易顺序为: 平纹、斜纹、缎纹。在组织结构上分析,起毛效果与纬浮点数、纬浮线长度,织物结构的紧度有关。纬纱浮点多,起毛容易,但落毛多,强降大。纬纱浮点长度长,浮于布面的纬纱线量多,经纱对纬纱的压力少,起毛容易。织物结构紧度大,纬纱的屈曲程度大,纬浮点突出布面,容易起毛。
(3) 染整工艺。织物起毛前需要经过退煮漂前处理工序、印染、化学整理等工序。为了保证起绒顺利进行,需要对以上工序进行合理的安排和控制。
①前处理: 前处理的原则是重退浆、轻煮练、适当加重漂白。退浆后织物结构松弛,手感柔软,易于起毛。蜡质的存在可以降低摩擦系数,起毛容易。所以充分煮练的织物难于起毛。漂白时严格控制织物强力,如果强度损失大,起毛难度大。丝光棉初始模量大,不容易起毛,绒毛短,但弹性好。对于仿麂皮棉织物可先丝光后起毛,产品绒毛短匀、富有弹性而有别于其他绒布。对于一般的绒布产品来说,要求绒毛柔而长并容易起毛、出绒,因此不做丝光处理。
②印染: 染料种类、浓度、上染条件、助剂等对起毛都有影响。实践证明: 棉用直接染料染色时,非离子缓染剂存在会增加纤维间摩擦系数,使起毛困难。通常染浅色时,缓染剂用量多,因此浅色织物难起毛。
酸性染料染色时,降低 pH 值有利于染色。织物上残留的助剂如食盐、硫酸钠、磷酸二氢钠等都可以增大纤维间的摩擦系数,如果含量多,则起毛困难。
③后整理: 织物经柔软剂或润滑剂处理后有利于起毛。研究表明: 离子型柔软剂可降低摩擦系数,适合用作起毛柔软剂。阳离子型柔软剂效果好于阴离子型柔软剂。非离子柔软剂多数增大摩擦系数,对起毛不利。
织物经过树脂整理后,由于整理剂在纤维内部交联或沉积,增大摩擦系数,造成起毛困难。对于采用某些交联型整理,可以考虑将交联反应放在起毛后进行。也可以增加起毛次数。具体工艺流程为:
浸轧整理剂→烘干→起毛→焙烘
(4) 设备因素。起毛机的型号,针布辊的根数和直径,针布材料和钩针锋利程度,钢丝号数、针杆长度、针密度等的合理选择也是保证起毛效果良好的重要因素。
4. 起毛工艺分析
(1) 起毛方法: 包括干起法、湿起法和水起法。
①干起法。指织物在干燥状态下起毛,这种方法应用最普遍。干态下,纤维刚性大,针布对织物作用力大。棉型织物、黏胶织物、粗纺毛织物如毛毯和大衣呢等均采用干法起毛,钢丝起毛机可以用于干法起毛。
②湿起法。指织物在润湿状态下起毛。此时,纤维刚性小,起毛力缓和。刺果起毛机和钢丝起毛机都可以用于湿法起毛。
③水起法。指将织物浸在水中,带水直接起毛。一般用于刺果起毛机对羊毛的起毛。
(2) 含湿率。纤维素纤维在干态下利于起毛,棉织物起毛时,含湿率控制在 6. 5% 左右效果好; 黏胶织物起毛时,也应保持相对低的含湿率,具体可以根据试验效果确定。毛织物在含湿率较高的状态下,起毛效果好,通常控制在 60% ~ 70%,以手摸上去不是水淋淋而是湿漉漉的感觉为宜。含湿率对化纤织物起毛效果影响不大。
(3) 织物张力。起毛时,布面的张力大小直接影响起毛效果。布面张力大,针辊所受的阻力大,起毛力小,所起的毛绒短; 张力太小,会引起起毛不匀和外观恶化。另外,经向张力大小均匀,可以保证起毛均匀。
(4) 起毛次数及布速。通常采用分步起毛的方式,起毛的力度由弱逐渐变强,这样起出的绒毛厚密,也可以避免一步法强起毛给织物纤维带来的过度损伤。降低起毛力,同时增加起毛次数,有利于拉出短、密、匀的绒毛; 提高起毛力,同时减少起毛次数,拉出的绒毛稀疏、长。
起毛布速慢,起毛力大,但生产效率低,此时,可以适当考虑减少起毛次数。但需注意,起毛次数太少,绒面效果不好。布速一般控制在 5 ~20m/min。
(5) 顺针辊和逆针辊的组合。从起毛效果来看,顺针辊(PR) 适合起长绒,逆针辊(CPR) 适合起短绒。操作上如果使逆针辊支撑织物,加大顺针辊的速度,使顺针辊深度起毛,可得到长绒毛,反之可得到短绒毛。当顺针辊速度过低时,织物易于朝着出布辊方向推移和堆积,造成织物运行时出布慢、进布快,织物不能紧贴于起毛大滚筒,并容易轧入针布辊中损坏织物。所以,工艺上合理协调控制顺针辊、逆针辊的速度很重要,一般 VPR∶ VCPR为 1∶ (1. 2 ~1. 5) 。
(6) 零点的调节与控制。零点分为机械零点(理论计算零点) 和上机零点。机械零点是指顺、逆针辊的针尖与织物的接触点,在切线方向上合速度为零时的机械状态,这是起毛设备设计、调试和正常运行的参考基准。上机零点是指顺、逆针辊的针尖对织物产生最小梳毛和最小起毛作用时的上机机械状态,这是上机工艺调节的参考基准。
在上机零点状态时,由于起毛钢针的变形、张力作用和织物在针布辊上的包绕弧等因素,导致针尖与织物的接触点产生相对位移差,从而对织物起毛产生影响。从结构上看,织物在此时厚度增加和绒面效果的产生,主要是纬向收缩和纱线受到疏松作用的结果,而不是起毛作用所致。这种状况重复次数越多,则针尖在进出织物时损伤纤维的概率越大,造成织物纬向强力减小。不同织物对应不同的上机零点,但其机械零点都是一致的。随着起毛设备的使用,针布更换和起毛工艺参数的调整,会导致机械零点和上机零点产生漂移,所以事实上,起毛工艺操作都是以上机零点为基准,掌握好上机零点状态,就可以制订准确的上机工艺,从而获得满意的绒面效果。
5. 常用起毛产品的生产工艺流程
(1) 纯棉中浅色单面绒产品的生产工艺流程。
翻布→缝头→碱退煮一步→漂白→(丝光) →染色→烘干→柔软整理→烘干→起毛→后处理→成品
纯棉绒布具有吸湿性高,柔软、厚实、保暖的特点,适合作内衣、睡衣、童装等。中浅色品种采用先染色后起毛的工艺。
为了保证绒布质地柔软、手感丰满、易于起毛,且强力损失小,纬纱要粗些,经密和纬密不宜高,捻度要小,棉纤维等级不要太高。如下的坯布规格比较适合起毛: 28tex ×28tex 斜纹布,幅宽96cm,经纱密度 157 根 /10cm,纬纱密度 165 根 /10cm。
起毛前,一般要浸轧柔软剂或者上蜡处理,这样可以增强起毛过程中的润滑作用,降低摩擦系数,有利于起毛钢针的插入和脱离。
(2) 纯棉双面绒印花产品的生产工艺流程。
翻布→缝头→碱退煮一步→氧漂→烘干→柔软整理→烘干→起毛→定形→上浆→印花→后处理→成品
纯棉双面绒印花产品要求绒毛短、密、匀,缩水率小,特别要保证织物的强力。为了便于起毛,还要保证织物在练漂后有一定的白度和渗透性,可采用轻煮练的前处理方法,一般练漂半制品的毛效控制在 7 ~8cm/30min 为宜。另外,由于双面绒织物厚,难以烘干,故加工时车速不宜快,可以采用复烘的方式。上浆是为了保证花型轮廓清晰,提高印花质量和效果。绒布水洗后一般采用上轻浆(淀粉浆 10g/L) 的工艺,将表面的绒毛粘压一下,绒毛压倒,表面平整,便于印花。上浆太厚则手感发硬,会给印花带来困难。
(3) 涤/棉中浅色起毛产品的生产工艺流程。
翻布→缝头→精练→漂白→染色→烘干→起毛(剪毛) →定形→成品
6. 起毛产品的效果评定 起毛效果评定有感官评定法和仪器测定法。一般起毛后绒毛的密度、长度、光泽、均匀度、手感、遮覆性等常用眼看手摸的感官法予以判定。而强力、厚度、弹性等指标则采用相应的仪器测定。
二、磨毛整理
1. 磨毛设备 目前,磨毛机有砂磨机(利用金刚砂粒) 和金属辊磨毛机(利用金属尖刺,又称磨粒) 两类。
(1) 砂磨机。砂磨机是利用表面粘有尖锐锋利的金刚砂粒的砂纸反复摩擦织物表面,使织物表面产生短、密绒毛,完成磨毛整理的。按砂纸在设备上的工作状态,分为砂辊式和砂带式磨毛机两种。其中砂辊式磨毛机,是国内大多工厂所采用的,而砂带式磨毛机应用较少。
①砂辊式磨毛机: 将不同粒度的砂纸紧紧包覆在可转动的导辊上,制成砂辊,通过转动的砂辊与织物的摩擦来完成磨毛过程。
砂辊式磨毛机主要由砂辊、张力调节辊、轧布辊、吸除尘装置、进出布装置,传动装置等组成,如图 2-23 所示。
图 2-23 砂辊式磨毛机结构简图
1—张力调节辊 2—砂辊 3—轧布辊
4—吸除尘装置 5—织物 6—传动装置
砂辊是主要的工作件。砂辊式磨毛机有单辊,也可以是多辊,目前应用较多的是多砂辊磨毛机,砂辊最多可达 6 个以上; 一般采用卧式排列,也可以是立式排列。砂辊可以任意升降位置。配合张力调节辊的使用,可以调节织物与砂辊的包覆角,改变砂辊与织物的接触状态,对不同品种、不同厚薄织物的磨毛程度进行合理的控制。砂辊是分别驱动的,速度可以独立调节,正反转均可。在工作 时,砂 辊 内 可 通 流 动 冷 水降温。
张力调节辊通常位于砂辊两侧,用于调节织物与砂辊的包覆角,控制磨毛程度。
刷毛辊位于砂磨的后序,用来去除织物上的磨屑,保持绒面清洁。吸除尘装置通过真空吸尘作用,将机器内部的磨屑全部吸出机外,防止污染环境。轧布辊位于砂辊的上方或下方,可上下移动,调节织物与砂辊之间的间隙,控制磨毛作用力。
②砂带式磨毛机: 砂带式磨毛机是将磨毛砂纸紧贴在无接缝的环形导带上,制成可循环运行的砂带,并使之与织物表面接触,进行磨毛加工。
砂带式磨毛机主要由环形砂带、主驱动辊、压辊、包覆角调节辊和刷毛、吸尘等装置组成(图 2-24) 。该设备主体为皮带传动系统,由主驱动辊环状砂带循环运行。通过改变包覆角调节辊的位置,增大或减小砂带织物接触面积,控制磨毛程度。
(2) 金属辊磨毛机。金属辊磨毛机与砂磨机的工作原理、组成结构相同,都是通过摩擦使织物起毛; 只是磨毛辊不同。金属辊磨毛机是利用金属磨毛辊,金属辊面上直接铸有密集锋利的小磨粒; 工作时与织物接触,进行磨毛加工。它具有磨毛效果稳定,产生绒毛稠密,质量好,可赋予柔软、蓬松的手感等特点; 特别是辊上的金属磨粒的耐磨性远优于砂纸,可以长时间保证良好的磨毛效果,适于大批量生产。
图 2-24 砂带式磨毛机结构简图
1—主动辊 2—砂带 3—张力辊 4—轧辊
5—包覆角调节辊 6—织物
但这种磨毛机结构相对复杂,投资成本高,尤其在磨毛过程中会产生大量的摩擦热,使磨毛辊温度升高。此时若加工涤纶等合成纤维织物,高温的磨毛辊会使纤维发生熔融,以至不能磨出理想的绒毛。同时大量的纤维熔融会堵塞和黏附在磨毛辊,大大降低金属磨粒的锋利程度,使磨毛效率大幅度下降。
2. 磨毛原理 磨毛加工是利用随机密集排列的尖锐锋利的磨料(金刚砂或金属磨粒) 摩擦织物表面,对织物进行削磨加工。工作时,高速运转的砂磨辊(带) 与织物紧密接触,磨料刀锋棱角先将织物纱线中纤维拉出,并切断成 1 ~2mm 长的单纤维,然后依靠磨料的进一步高速磨削作用,使单纤维形成绒毛。随着磨削过程的进行,织物上长短不一的绒毛趋于磨平、一致,形成均匀、密实、平整的绒面。
磨毛织物的绒毛细、密、短、匀,有皮革的平滑细腻感和舒适感,其性能优于起毛织物。另外,磨毛产品还改变了织物外观,消除了织物表面的极光。而起毛产品的绒毛长,感觉厚重,且绒毛刚性强,对皮肤有一定的刺激性。
3. 影响磨毛效果的因素
(1) 磨粒和砂皮: 作为直接摩擦织物的材料要有较高的硬度、耐磨性、耐热性,保证加工性能良好的尖锐锋利的棱角。
作为磨粒的材料有氧化物、碳化物和高硬度材料(天然或人造金刚石材料) 等,其中氧化物和碳化物应用最广。
磨粒的几何形状是随机的,颗粒大小以粒度表示。粒度号大,磨粒实际尺寸越小。
一般轻薄织物起短绒,采用柔和高号数的砂皮; 厚重织物起长绒,采用摩擦剧烈的低号数的砂皮。
(2) 砂磨辊与织物的运行速度: 磨毛时,一般砂磨辊表面的线速度大大高于织物的运行速度。
两者速度差大,织物与砂磨辊接触时间相对长,织物表面越易形成短、密、匀的丰满绒毛,磨毛效果好; 但布速不能太慢,否则织物会受到过度摩擦,强度下降严重,严重的甚至磨破。反之两者运行速度相近则产生稀而长的绒毛,织物强降少,手感较硬。对于粗厚织物,砂磨辊的速度可以高些,而轻薄织物宜低些。砂磨辊转速和布速可以分别调节的,一般砂磨辊在 800 ~1500r / min,布速在 10 ~ 20m / min 范围内。
另外,砂磨辊转动方向对磨毛效果有影响。当砂磨辊回转方向与织物运行方向一致时,磨毛作用小,磨毛柔和; 当两者的方向相反时,磨毛效果好,但织物强降大,操作难度增加,故一般反转砂磨辊不宜多用。
(3) 织物与砂磨辊的接触程度: 织物与砂磨辊接触后形成包覆角。包覆角越大,织物与砂磨辊接触面积越大,磨毛作用显著,效果好。但织物强力下降大,严重的会磨破织物。包覆角的大小是通过轧布辊的压力控制。通常织物与砂磨辊接触弧长为 1 ~1. 5cm,绒毛基本可以达到要求。同时,必须恰当地控制好车速和接触弧长,否则会造成磨毛不良或织物强力下降过多。一般强力下降控制在 15% ~20%为宜。
(4) 纤维和织物结构: 纤维不同,磨毛后力学性能差异很大。合成纤维强度高,磨毛难度大,容易起球,磨毛效果差,强度降低少。纤维素纤维强度低,含杂质多,纤维容易起毛,并获得良好的磨毛效果,但强度损伤大。纤维长度短,起毛容易。
织物中纱线捻度高,经纬密度大,不容易磨毛。通常磨毛产品的坯布纱线捻度要降低10% ~ 15% ,这样有利于磨毛。
磨毛时磨粒对经纬纱的磨削概率是相同的,但纬纱受到磨粒垂直的削磨作用,所以磨粒对纬纱的磨削作用大,纬纱磨损大。对于稀薄织物,磨毛后强力损失大,容易造成纬纱移位,磨毛难度大,一般采用高号数砂皮磨毛。中厚织物、提花织物、条纹织物、卡其类织物等纬纱浮点多,相对容易磨毛,常选择低号数的砂皮磨毛,产生的绒毛浓密、长而匀。
(5) 织物张力控制: 张力的大小决定了织物与砂磨辊接触时绷紧的程度和磨粒刺入织物的深度。在一定范围内,随着张力的提高,织物绷紧,布面与砂磨辊接触越紧密,嵌入织物的磨粒越多,嵌入深度越大,磨毛作用增强,磨毛效果好。但当张力达到一定值后,由于嵌入织物的磨粒趋于饱和,数目不再增加,故磨毛效果已经无多大改善,如不改变其他参数则磨毛效果不会提高,张力太大反而织物断裂强度下降。
实践证明,对中厚密织物强力可以大些,以 0. 4MPa 为宜; 对稀薄织物张力宜小些。
(6) 轧布辊与砂磨辊的隔距: 轧布辊与砂磨辊之间的隔距,一般略大于织物厚度 0. 1 ~0. 3mm,这样既可以保证织物顺利进入摩擦点,又能使织物磨毛。
(7) 磨毛次数: 多次磨绒可以提高磨毛效率,磨毛效果好。但织物强力随磨毛次数增加而下降,所以应根据织物所承受撕裂程度和所需毛感的实际情况而定。
(8) 染整加工工艺: 染色织物经过磨毛后颜色一般变浅。若织物磨毛后再进行染色,则选择颗粒细的染料。染料颗粒细,渗透性好,纤维容易透染,纤维内部上染较多,经过磨毛后正反色差小。反之,若染料颗粒粗,则使纤维表面着色多,磨毛后织物正反色差大。
织物经过树脂整理后,会使磨毛加工有一定困难,但可以提高织物绒毛的抗压性。为了解决此问题,可采用浸轧树脂整理工作液→烘干→磨毛→松式焙烘; 若在树脂整理后再加一次轻磨毛,则磨毛效果更好。
4. 常用磨毛产品的生产工艺流程
(1) 纯棉或者含棉混纺织物的生产工艺流程: 根据磨毛织物品种,烧毛一般为一正一反、轻烧或只烧反面。本色布、漂白布和浅色布可不丝光。对于先染后磨或先磨后染工序的选择,通常与织物颜色的深浅有关。一般来说,对于中浅色织物如浅灰色、淡黄色、浅粉色等,采用先染后磨工艺,可使正反面色差小,绒面色光无变化; 对于深色织物如深蓝色、藏青色、墨绿色、黑色等,应先磨毛后染色,否则极易产生正反面色差。目前,很多企业在实际生产中,无论颜色深浅,全部都采用先磨后染工艺。另外,磨毛后染浅色可不进行染色前的水洗(因染色机进布前有吸尘装置,可吸除布面绒毛) 。
①本色磨毛织物:
翻布→缝头→烧毛→退、煮、漂→柔软整理→(定形) →(丝光) →打卷→磨毛→(防缩) →成品
②漂白磨毛织物:
翻布→缝头→烧毛→退、煮、漂→复漂→柔软整理→(定形) →(丝光) →打卷→磨毛→柔软拉幅(兼加白) →(防缩) →成品
③中浅色磨毛织物:
翻布→缝头→烧毛→退、煮、漂→(定形) →(丝光) →染色→(后定形) →柔软整理→打卷→磨毛→柔软拉幅→(防缩) →成品
④深色磨毛织物:
翻布→缝头→烧毛→退、煮、漂→(定形) →丝光→(打卷) →(亲水柔软整理) →磨毛→(水洗) →染色→(后定形) →柔软拉幅→(防缩) →成品
(2) 涤/棉织物磨毛产品的生产工艺流程:
松弛前处理→预热定形→碱减量处理→皂洗→松式烘干→染色→柔软烘干→磨毛→水洗→柔软、拉幅定形→成品
涤/棉织物经过磨毛后消除了涤纶的蜡状手感,使涤/棉织物穿着舒适感明显好转。预热定形温度不能太高,过高会使织物结构太稳定,导致磨毛困难。深色品种也采用先磨后染的工艺路线。
碱减量处理可以使涤纶表面具有多孔性并产生凹穴,降低了涤纶的刚性,提高了织物的悬垂性,并有丝绸般的手感,吸湿性提高。
(3) 超细涤纶桃皮绒产品的生产工艺流程: 以中浅色产品为例。
前处理→碱减量处理→定形→染色→柔软整理→磨毛→砂洗→柔软整理→拉幅定形→成品
在染整加工中,需要用化学或者物理方法将复合纤维分开,才能形成超细纤维,这个过程称为开纤。通常使用的是化学方法即碱减量处理,在碱的作用下复合纤维溶胀、膨化,并产生分离,从而形成超细纤维。另外,碱减量处理可以使涤纶超细纤维获得常规涤纶经碱减量处理后的效果,表面具有多孔性并产生凹穴,使手感柔软,提高吸湿性。
碱减量处理后,纤维表面有很多裸露的微纤,若在松弛状态下使纤维膨化疏松,配合磨毛砂洗—柔软剂处理,即可使这些裸露于织物表面的微纤竖立起来,得到手感丰满的桃皮绒产品。超细桃皮绒产品工艺流程详细描述可见学习任务 7-4 仿桃皮绒整理。
(4) 超细涤纶仿麂皮产品的生产工艺流程:
松弛前处理→预热定形→碱减量处理→起毛→剪毛→染色→浸轧聚氨酯涂层液→湿法凝固→水洗→柔软烘干→磨毛→水洗→柔软、拉幅定形→成品
超细涤纶用聚氨酯涂层加工后,再经过磨毛处理,可以获得仿麂皮的效果。具体工艺详见“学习任务 7-5 仿麂皮整理”。
5. 磨毛产品的质量评定 磨毛之后的产品无论手感和毛感都有很大的提高: 磨毛之后,织物的组织相对蓬松且手感柔软; 毛感相对比较均匀,而毛的疏密长短,则是根据来样的要求而定的。
通常,测定磨毛产品质量的方法根据肉眼观察和手摸,要求比较高的可用放大镜来观察。织物经磨毛后,应注意观察是否有边差,即两边和中间的毛感是否一致; 还要检查织物的强度,主要是撕裂强度是否能达到要求。
织物经磨毛后,有的无须定形(机织物) ,有的则要定形(针织物) ; 不一样的织物磨出来的毛感也不一样,但结果都是为了提高织物的使用舒适度。
三、起毛和磨毛的比较
起毛织物的绒感比较厚实,绒毛较长; 磨毛则强调的是毛感,相对于起毛来说,磨毛织物的绒毛比较短。