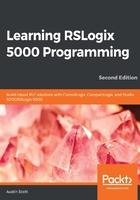
Controlling equipment with water, air, and power
The earliest control systems can be traced back to the float regulator mechanisms that were used in Greece around 270 BC. The need for accurate time tracking inspired the Greek water clock (clepsydra), which leveraged the simple float regulator to maintain a constant flow of water. The float regulator would maintain the water level in a primary tank at a constant depth; water kept at a constant depth maintained a constant water pressure.
Constant pressure resulted in a constant flow of water through a tube that would fill a secondary tank at a constant rate. The level of the second tank was used to measure time, which was displayed on a dial using a second float. A similar float regulator mechanism is still used in our toilets today. A construct that uses input from another device (float) to maintain a value (water level) is called a feedback controller.
The following diagram details the components of a simple Greek water clock (clepsydra):

In the next section, we will discuss the advent of pneumatics and its place within industrial control systems.
The rise of pneumatics
The Greeks also invented a more sophisticated feedback control mechanism that utilized steam or compressed air, rather than water, called pneumatics. The Greek mathematician Hero of Alexandria created inventions that were powered by steam or the wind. German physicist Otto von Guericke (1602 – 1686) was the first to invent a vacuum pump that can draw out air or gas from the attached vessel. After the industrial revolution, the air pressure from pneumatics was used as a method of activation and signal transmission within control systems. In the 1950s and 1960s, pneumatics signal transmission started to be replaced by electric signal transmission, which gave rise to the modern control systems we see today. However, it is not uncommon to see pneumatics still used today in a wide range of applications. Today, pneumatics are still a ubiquitous part of many Heating Ventilation and Air Conditioning (HVAC) systems.
The following diagram illustrates a typical pneumatic HVAC heating system (image courtesy of Spirax Sarco Limited):

The preceding diagram shows how a pneumatic controller is used to regulate the temperature of a steam heating system using a pneumatic temperature control valve based on the feedback loop from the temperature sensor.
In the next section, we will introduce the electromechanical relay and discuss how it changed industrial automation forever.
Understanding electric relay logic
The electromechanical relay was first created in 1835 by Joseph Henry (1797 – 1878). Although Joseph Henry built and demonstrated the first mechanical relay, he had no intention of applying it to a practical application. The relay was used to demonstrate the phenomenon of self-inductance and mutual inductance to his students. In 1836, when Samuel F. B. Morse learned of the electromechanical relay, he began to consider its potential application for communications and controlling machinery.
Samuel Morse soon used Henry's relay device to carry morse code signals over long distances of wire. As electromechanical relays began to be widely adopted to control electrical equipment, a standard method of documenting the relay wiring was required. This led to the advent of ladder diagrams, which were used to document the convoluted logic of these systems so that they could be maintained and upgraded.
Control systems evolved into a complex mixture of industrial relays, rotary drum sequencers, pneumatic plunger timers, counters, motors, push buttons, selector switches, limit switches, and valves, all connected together and controlled using hundreds or thousands of failure-prone electromechanical relays. As complex control systems evolved and were maintained, they inevitably transformed into a rat's nest of wires, leading to outages and extended turnarounds. General Motors (GM) had grown tired of the shortcomings of hardwired relay logic within their automotive factories and were aware of advances in solid-state computers. So, as the story goes, on New Year's Day 1968, they detailed a specification for what would later be known as the Programmable Logic Controller (PLC). GM’s requirements were as follows:
- Competitively priced with a traditional relay logic system
- Leveraging a solid-state system that is flexible, such as a computer
- Programmed in a manner that aligns with accepted relay ladder engineering diagrams
- Robust enough to work in industrial environments where they would be exposed to dirt, moisture, electromagnetism, and vibration
- Modular and expandable to support a wide range of process sizes and types
We have now covered the past 2,000 years of industrial automation evolution. In the next section, we will introduce Rockwell Automation and detail their contributions to the automation industry.